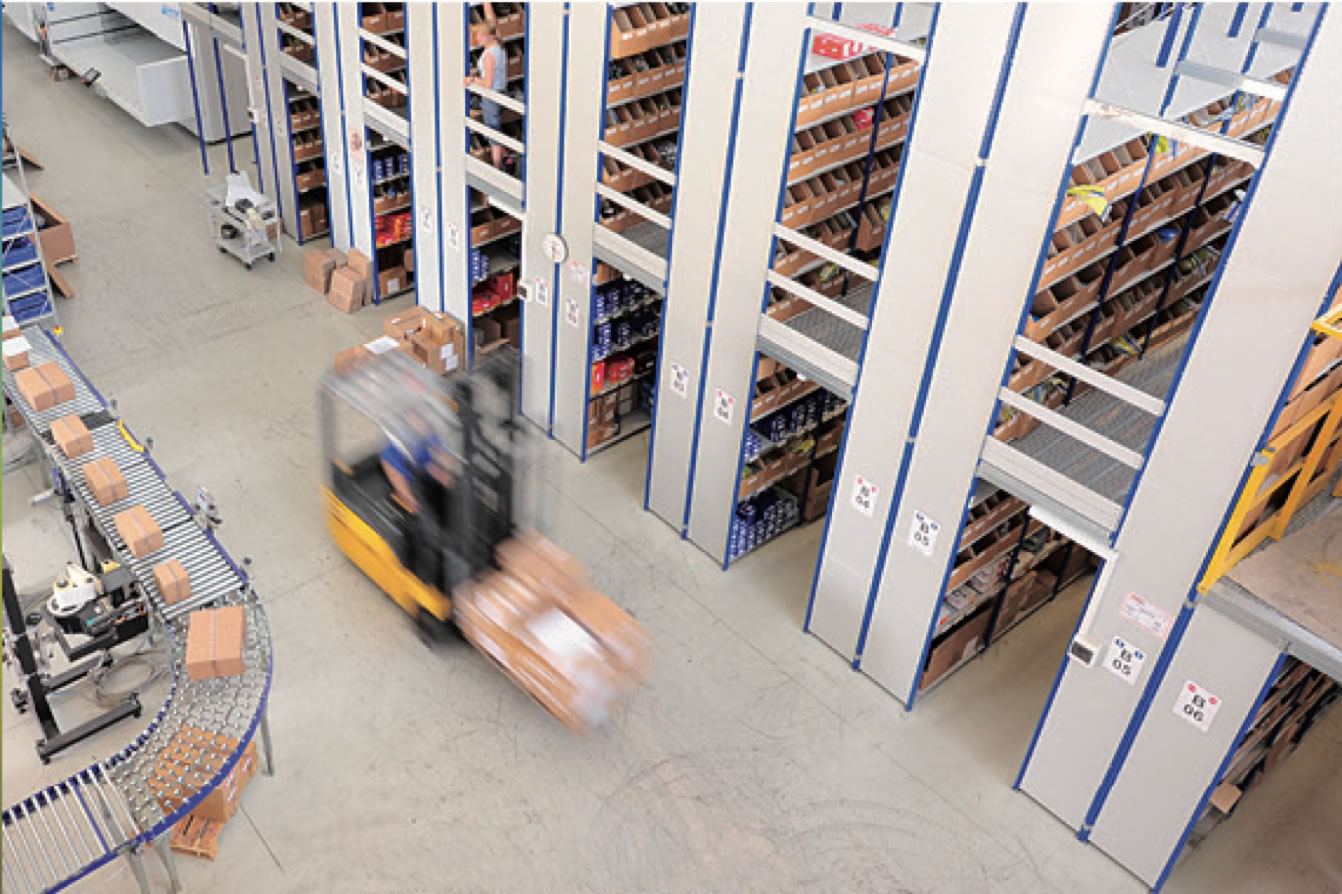
- Automotive
- Case Study
Malò: an integrated system to support growth with management, logistics and business intelligence
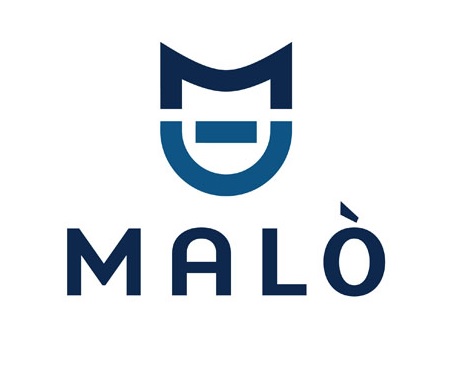
With 112 employees and a customer base of more than 3,500, Malò Spa deals with more than 60,000 parts, between its Milan headquarters and its distribution network, with 4 branches + 10 warehouses in Italy and 2 abroad, for a total of over 300,000 orders and 35 million parts handled every year.
These are truly impressive figures and, what is more, they are growing all the time.
Until 1997, the company’s entire IT processes were handled in-house by a single programmer.
The company's plans for growth, which include an increased focus on sales, logistics and products, gradually made the adoption of a fully available, dynamic and efficient solution absolutely necessary. Starting with accounting, which as a standardised activity can be adopted without impacting the company’s processes, Malò ran a software selection tender to identify a more up-to-date solution.
The choice fell on Sisthema Spa, with its flagship product SoftwareSirio. After a few years, Malò's needs increased: it had to be able to evolve more dynamically without being held back by its own structure. The software used up to that time, which had been developed in-house, proved to have reached its limits, and the company decided to outsource its IT processes in their entirety. Satisfied with its existing collaboration, Malò thus entrusted Sisthema with a much more ambitious project than the original one, with the aim of being more dynamic and in step with the times, as well being able to concentrate on its core business: the development of its own products. Furthermore, as it was designed to manage only one branch, Malò’s in-house software was now impractical and inefficient in view of its on-going growth, with the number of branches continuing to increase; the programs used at the various branches now had to be integrated with each other, so as to provide a full overview of the company’s data.
The time had also come for a specific Business Intelligence solution, to enable better use of data and ability to query and process information with a variety of views. Speaking of logistics - an extremely strategic issue for Malò - there was also the need to optimise warehouse space, to interface with its machinery (automatic weighing, shifters, etc.), track transactions (up to and including movements per bin), as well as to interface with external solutions for exchanging data with external warehouses.
Driven by these new requirements and aware of the unquestionable advantages of having a single point of contact, Malò once again chose Sisthema, which has now become a strategic partner for the company; in fact, over time, Sisthema has got to know Malò, its complexities and objectives to perfection, and has provided many suggestions for developing its business and improving its processes.
In order to meet Malò's different needs, Sisthema installed SoftwareSirio V10 (initially only in accounting, later in all areas of management), integrated with Business Intelligence and CRM solutions. The configurability of SoftwareSirio’s commercial modules enabled Malò to satisfy new commercial policy requirements for the purchasing and sales areas in the automotive product distribution sector, and integrate data that was not available in the previously installed software.
SoftwareSirio’s modules for managing logistics have been implemented, thanks to their integration and customisation functions, so as to integrate logistics processes with the logic of optimised article locations and picking times. In addition, devices such as radio frequency terminals, shifters, vertical magazines, packaging chains and weighing detection systems have been interfaced with and integrated into the processes, which are now completely interactive with SoftwareSirio, thus enabling tracking of product movements down to the individual bin by location.
The configurability of Webgate400 was leveraged to profile internal and external users (connection to external clients) in a timely manner to consult the data in the system with the utmost respect for the company's privacy and confidentiality guidelines. Finally, by adopting the BOARD Business Intelligence tool, reference to the multiplicity of data present provided by SoftwareSirio has been facilitated and made modifiable in terms of display, sorting and hierarchization directly by the user; SoftwareSirio V10 has enabled integration of administrative and management processes with local and international procurement processes; advanced production management with scheduling and progress monitoring; subcontractor management which involves the subcontractor in updating the company information system with natively web-based applications; management control and analytical cost accounting; and finally the marketing / CRM area and Business Intelligence.